When kitchen tech inventor Scott Heimendinger started prototyping his latest hardware product, he knew that much of it would need to be built overseas. Still, he was curious whether he could rely on local Seattle-based shops to produce some of the parts.
“I contacted local shops here in Seattle. There are a couple of machine and metalworking shops, and I thought, well, I would like to be a good customer, right? Like I’d love to spend money locally, especially on shops that are doing this kind of stuff.”
But when he called around, Scott quickly discovered that not only were the local shops going to be an order of magnitude more expensive, but they’d also take longer to deliver.
“I said, ‘look, I know this is going to be more expensive than what I’m doing in China, obviously, but maybe we can make this up on the time front.’ Before we even got into real pricing, we were already above 10X. So I said, ‘What about turnaround time?’ [They] said, well, it depends how busy we are, but like, you know, one to six weeks.’”
We’d started talking about the cost and complexity of building in the U.S. because we’d both recently listened to an episode of PJ Vogt’s Search Engine, in which Vogt interviewed YouTuber and engineer Destin Sandlin. Sandlin discussed his years-long effort to manufacture a product in America, and I wanted to get Scott’s take, especially since he’s been navigating the uncertainty caused by new tariffs. As it turned out, he had a lot to say.
One area he pointed to as a critical missing link was the shortage of tooling designers, the specialists who create the molds used to shape plastic parts.
“Tooling fabrication in principle is something that you could just do on a beefy CNC machine… In practice, no. It’s specialized techniques and tools. That knowledge has dried up in the U.S.”
We talked about why capabilities like tooling fabrication and injection molding have largely disappeared from the U.S., and one reason we both agreed on was the lack of trade education, starting as early as high school.
“Some of my favorite classes in high school were sculpture class, learning to use a bandsaw and a drill press,” he said. “I wish more folks in the United States prioritized the hands-on making of stuff.”
I pointed out the strange dichotomy of the past couple of decades, in which Silicon Valley was busy valorizing the maker movement, while at the same time the U.S.’s ability to manufacture at scale was simultaneously being hollowed out. It’s as if we celebrated prototyping, while the infrastructure to mass-produce those ideas was quietly de-emphasized and disinvested in.
“A weird thing that happened, where we talked about, ‘hey, let’s start making stuff and teach our kids to make stuff,'” I said. “But at the same time, America’s ability to make stuff at scale just kind of went up in smoke.”
Scott, for his part, chose to see the upside. Despite the loss of critical manufacturing knowledge and infrastructure, he said it’s still a great time to be an inventor, thanks to how accessible prototyping tools have become.
“I’m of two minds about this. On the one hand, like I love physically making stuff. I wish more folks in the United States prioritized the hands-on making of stuff, and I wish that we hadn’t eroded away these capabilities. On the other hand, it is almost point and click to have these things prototyped, if not mass-produced. And that’s an incredible boon to being a scrappy solopreneur.”.
You can listen to our latest episode by clicking play below, or you can find it on Apple Podcasts, Spotify, or wherever you get your podcasts.
If you’d like to ask Scott a question about his project, the challenges of manufacturing a product or the future of cooking, he’ll be at Smart Kitchen Summit next week. You can get your ticket here.
If video is your preferred podcast consumption format, you can also watch our conversation below:
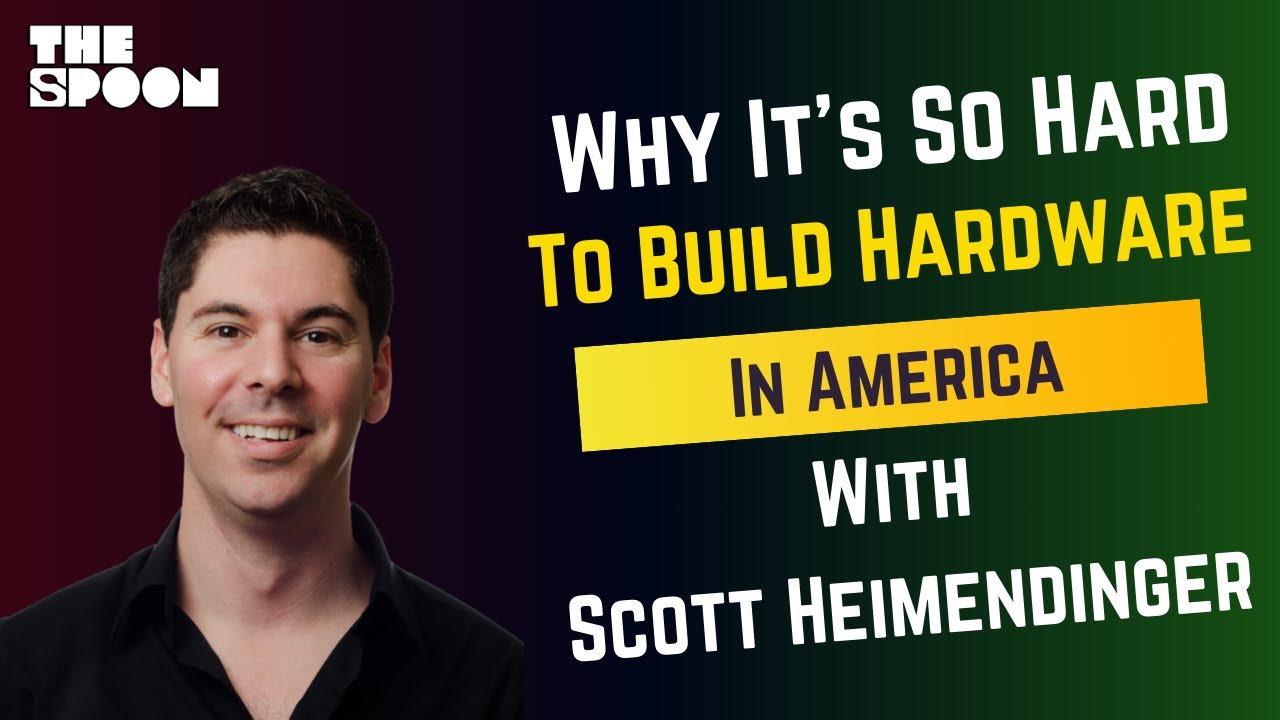
Did you miss our previous article...
https://ballerawards.news/epicure/leanpath-ceo-excited-for-potential-of-ai-to-drive-action-as-fight-against-food-enters-its-second-act